Category
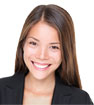
BLDC Motor Supplier

Home » BLDC Motor FAQ » How to Run a BLDC Motor in Forward and Reverse?
How to Run a BLDC Motor in Forward and Reverse?
DC motor has fast response, large starting torque and good speed regulation performance. There are two kinds of DC motors: Brushed DC motor and brushless DC motor. We know that brushless DC motor in many occasions not only requires the motor has good starting and adjusting characteristics, but also requires the motor can be positive and negative rotation. So how to realize the forward and reverse rotation of brushless DC motor?
Generally, the logic relationship of the inverter switch tube is changed, so that the phases of the armature windings are sequentially turned on to realize the forward and reverse rotation of the BLDC motor. In order to make the motor both positive and negative rotation can produce the maximum average electromagnetic torque to ensure symmetrical operation, it is necessary to design the position relationship between rotor position sensor, rotor main magnetic pole and stator phase windings, as well as the correct logical relationship.
Forward / Reverse Control (DIR) of BLDC Motor
The motor's running direction can be controlled by controlling the on and off of the terminals DIR and COM. Terminal "DIR" internal resistance to pull up to +12Ω, can be used with passive contact switch, but also with the collector open PLC and other control units. When "DIR" and terminal "COM" are not connected, the motor runs clockwise (facing the motor shaft), otherwise, it runs counterclockwise. In order to avoid the damage of brushless dc controller, when changing the BLDC motor steering, the motor should be stopped before the operation of changing the steering, to avoid the motor running direction control.
Speed Signal Output (SPEED) of BLDC Motor
The brushless DC controller provides the user with a pulse signal proportional to the brushless DC motor speed via the terminals SPEED~COM. Pulse per revolution =6 * motor pole logarithm, SPEED frequency (Hz) = pulse per revolution * SPEED (RPM) divided by 60. Example: 4-pole motor, 24 pulses per revolution, when the motor SPEED is 500 revolutions/min, the output frequency of terminal SPEED is 200Hz.
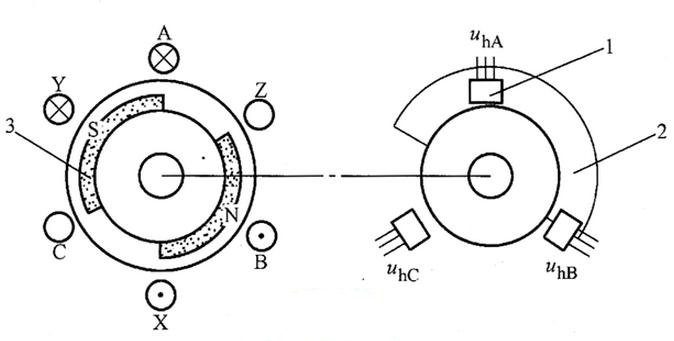
Generally, the logic relationship of the inverter switch tube is changed, so that the phases of the armature windings are sequentially turned on to realize the forward and reverse rotation of the BLDC motor. In order to make the motor both positive and negative rotation can produce the maximum average electromagnetic torque to ensure symmetrical operation, it is necessary to design the position relationship between rotor position sensor, rotor main magnetic pole and stator phase windings, as well as the correct logical relationship.
Forward / Reverse Control (DIR) of BLDC Motor
The motor's running direction can be controlled by controlling the on and off of the terminals DIR and COM. Terminal "DIR" internal resistance to pull up to +12Ω, can be used with passive contact switch, but also with the collector open PLC and other control units. When "DIR" and terminal "COM" are not connected, the motor runs clockwise (facing the motor shaft), otherwise, it runs counterclockwise. In order to avoid the damage of brushless dc controller, when changing the BLDC motor steering, the motor should be stopped before the operation of changing the steering, to avoid the motor running direction control.
Speed Signal Output (SPEED) of BLDC Motor
The brushless DC controller provides the user with a pulse signal proportional to the brushless DC motor speed via the terminals SPEED~COM. Pulse per revolution =6 * motor pole logarithm, SPEED frequency (Hz) = pulse per revolution * SPEED (RPM) divided by 60. Example: 4-pole motor, 24 pulses per revolution, when the motor SPEED is 500 revolutions/min, the output frequency of terminal SPEED is 200Hz.
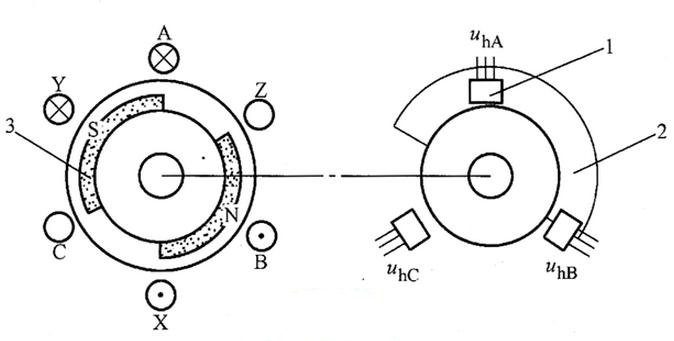
Worthless article
Post a Comment:
You may also like: