Category
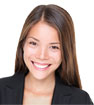
BLDC Motor Supplier

Home » BLDC Motor FAQ » How to Troubleshoot BLDC Motor Overheating?
How to Troubleshoot BLDC Motor Overheating?
Common overheating causes and treatment methods of brushless DC motor.
-
Overload. Load should be reduced or large capacity motors should be replaced.
-
Local short circuit or grounding of winding, local overheating of motor in light time, burning of insulation in serious time, emitting scorching odor or even smoking. The DC resistance of each phase of the winding should be measured, or the short-circuit point should be found, and the grounding of the winding should be checked by megohmmeter.
-
There are two kinds of external wiring errors in brushless DC motor:
(1) The Delta connection should be misconnected to the Y connection, so that the current is very small at no-load, while the light load can drive the load, but the current exceeds the rated value, so that the motor heating.
(2) The Y-connection should be misconnected to the delta-connection so that the current may be greater than the rated current at no-load, which makes the temperature of the motor rise rapidly.
For the above reasons, the wiring can be changed in the correct way.
-
The fluctuation of power supply voltage is too large. The fluctuation range of power supply voltage should be controlled between 5% ~ 10%. Otherwise, the load of motor should be controlled.
-
The core of stator and rotor is seriously dislocated. Although the no-load current is three-phase balanced, it is larger than the prescribed value. The position of the core should be corrected and fixed.
-
Brushless DC motor winding or wiring one-phase circuit break, so that the motor only works in two phases. Three-phase current should be checked and the power supply should be cut off immediately to find the breaking point and reconnect.
-
Rotor winding of winding motor is unsoldered or welded poorly, which results in overheating of the rotor and a significant decrease in speed and torque. The DC resistance of the rotor winding and the welding points can be checked and re-welded.
-
Motor windings are damped, or dust, grease are attached to the windings, so that the insulation is reduced. The insulation resistance of the motor should be measured and cleaned and dried.
-
The motor starts too frequently in a short time. The number of start-up should be limited and thermal protection should be selected correctly.
-
When the stator and rotor collide, the motor emits metal impact sound. The temperature of the iron core rises rapidly. In serious cases, the motor smokes and even the coil burns down. The motor should be disassembled to check whether there are traces of sweeping chamber on the iron core, find out the reasons and deal with them.
-
If the ambient temperature is too high, ventilation and cooling conditions should be improved or motors with higher heat resistance should be replaced.
- If the ventilation system fails, check whether the fan is damaged, whether the rotation direction is correct, and whether the ventilation duct is blocked.
Post a Comment:
You may also like: